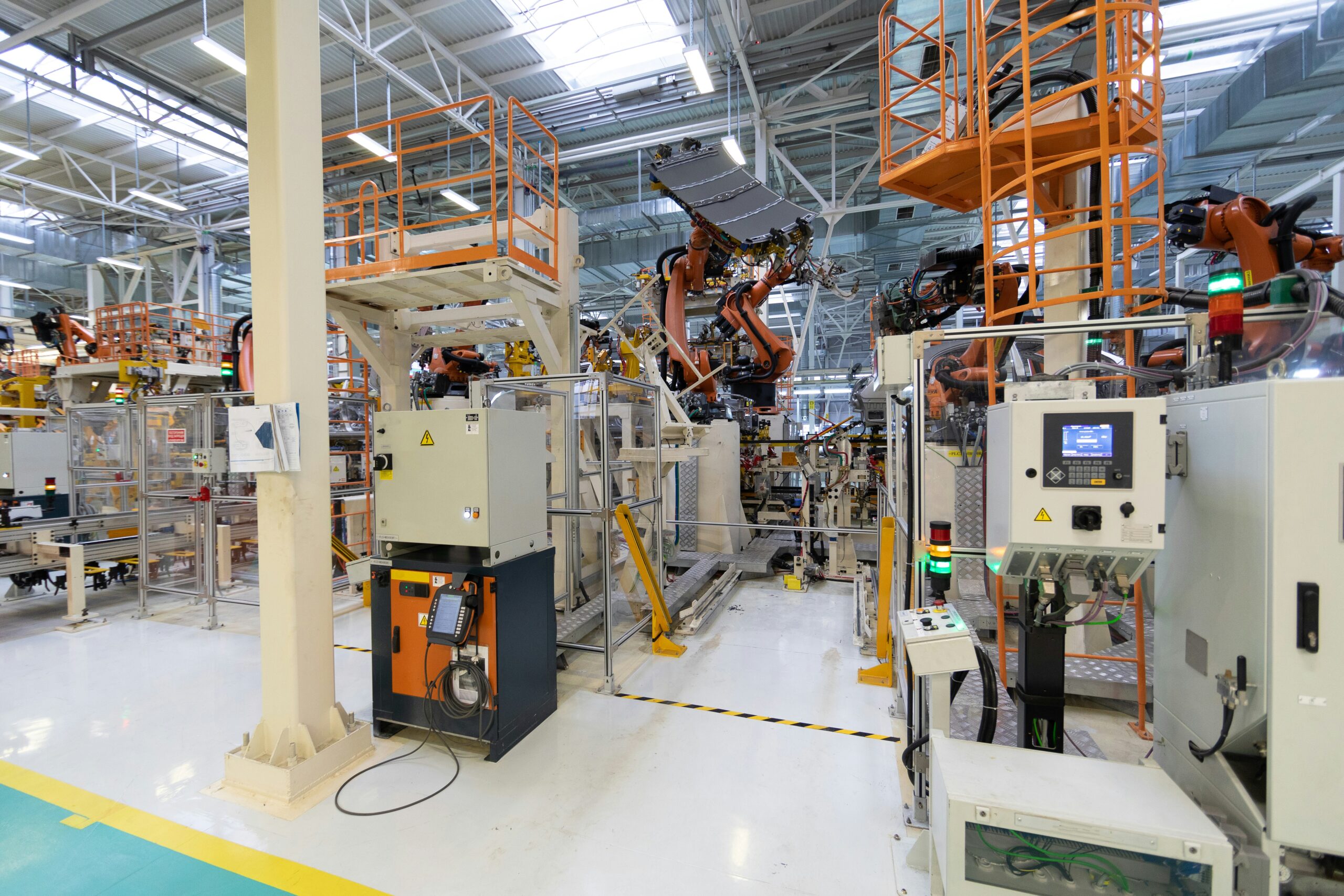
Manufacturing process innovation transforms industries by integrating cutting-edge technologies, improving efficiency, and reducing waste. Companies that embrace innovation gain a competitive advantage through lower production costs, enhanced productivity, and superior product quality.
Today’s industrial sector is evolving rapidly due to automation, smart manufacturing, artificial intelligence (AI), and sustainable production methods. This shift allows manufacturers to optimize operations, respond to market demands faster, and meet sustainability goals.
The Importance of Innovation in Manufacturing
Manufacturers must continuously improve their processes to remain competitive in a dynamic global economy. Innovation enhances productivity, reduces downtime, and ensures businesses can meet the evolving expectations of consumers and regulatory bodies.
Key Benefits of Manufacturing Process Innovation:
- Increased Productivity – Advanced automation improves production speed and efficiency.
- Cost Reduction – Optimized workflows reduce material waste and operational expenses.
- Higher Product Quality – Precision engineering minimizes defects and inconsistencies.
- Sustainability Improvements – Energy-efficient systems and eco-friendly materials help companies meet environmental regulations.
- Enhanced Flexibility – Agile manufacturing processes allow companies to quickly adapt to changing consumer preferences and market conditions.
Investing in modern technologies leads to long-term cost savings and ensures businesses remain resilient amid economic fluctuations.
Key Drivers of Manufacturing Innovation
Several technological advancements and methodologies contribute to the evolution of manufacturing processes. These drivers of innovation improve efficiency, product customization, and sustainability.
Automation and Robotics
Automation revolutionizes manufacturing by reducing dependency on manual labor and increasing precision. Robotics enhances productivity through:
- Repetitive task automation – Robots handle monotonous, high-volume tasks, allowing human workers to focus on complex problem-solving.
- Improved consistency – Automated systems ensure uniformity in product quality.
- Enhanced workplace safety – Robots take over hazardous tasks, reducing workplace injuries.
Industries such as automotive, electronics, and pharmaceuticals have widely adopted robotics to improve efficiency.
Artificial Intelligence and Machine Learning
AI-driven manufacturing solutions optimize processes by analyzing large datasets to detect inefficiencies and predict maintenance needs. Machine learning algorithms improve:
- Predictive maintenance – AI identifies potential equipment failures before they occur, minimizing downtime.
- Quality control – Automated inspection systems detect defects with high accuracy.
- Process optimization – AI-driven insights help manufacturers make data-backed decisions to improve production efficiency.
Companies leveraging AI reduce production costs while maintaining high-quality standards.
Lean Manufacturing Principles
Lean manufacturing focuses on eliminating waste and maximizing productivity. Key principles include:
- Just-in-Time (JIT) production – Reducing excess inventory and streamlining supply chains.
- Kaizen (Continuous Improvement) – Encouraging small, incremental improvements to enhance efficiency.
- Value Stream Mapping – Analyzing workflows to eliminate non-value-adding activities.
These strategies help manufacturers optimize resources and reduce unnecessary expenditures.
3D Printing and Additive Manufacturing
Additive manufacturing allows companies to produce complex components with minimal material waste. Advantages of 3D printing include:
- Rapid prototyping – Engineers can quickly test and refine product designs.
- Customization – Tailored production meets specific customer requirements.
- Material efficiency – Traditional manufacturing wastes raw materials, whereas additive methods use only what is needed.
Industries such as aerospace, healthcare, and consumer goods benefit from 3D printing’s flexibility and cost-effectiveness.
Smart Manufacturing and IoT Integration
The Industrial Internet of Things (IIoT) connects machines, sensors, and software, enabling real-time data analysis. Smart factories leverage IoT to:
- Monitor equipment performance – Detect inefficiencies and prevent breakdowns.
- Optimize energy consumption – Reduce waste through intelligent energy management.
- Enhance supply chain visibility – Improve logistics and inventory management.
IoT-driven manufacturing reduces operational costs while improving production efficiency.
Advantages of Implementing Process Innovation
Companies adopting modern manufacturing innovations experience significant benefits:
- Faster production cycles – Automated systems increase output and meet customer demands.
- Lower operational costs – Smart technology optimizes energy use and material consumption.
- Higher product quality – Advanced precision engineering minimizes defects.
- Sustainability improvements – Reduced waste and energy efficiency enhance environmental compliance.
- Greater adaptability – Companies can quickly adjust production to meet changing market trends.
Challenges in Adopting New Manufacturing Technologies
While manufacturing process innovation offers numerous benefits, companies often face challenges during implementation.
High Initial Investment Costs
Adopting new technologies requires substantial capital. However, long-term efficiency gains and cost reductions achieve a return on investment (ROI). Government grants and tax incentives can help businesses mitigate initial expenses.
Workforce Training and Skill Gaps
Advanced technologies require skilled workers who can operate and maintain automated systems. Companies must:
- Invest in employee training programs.
- Partner with technical schools to develop a skilled workforce.
- Encourage lifelong learning initiatives to keep employees up to date with industry advancements.
Cybersecurity Risks in Smart Manufacturing
As factories become more connected, they become vulnerable to cyber threats. Manufacturers must:
- Implement strong encryption and firewall protections.
- Regularly update software to prevent security breaches.
- Train employees on cybersecurity best practices.
Protecting intellectual property and sensitive production data is essential for maintaining a secure manufacturing environment.
The Future of Manufacturing Innovation
Emerging trends are set to redefine manufacturing, pushing industries toward smarter, more sustainable production methods.
AI-Driven Predictive Maintenance
AI-powered predictive analytics detect maintenance needs before equipment failures occur. This minimizes downtime and ensures smooth operations.
Sustainable and Green Manufacturing
Sustainability is a growing priority in manufacturing. Key trends include:
- Renewable energy adoption – Solar and wind power reduce reliance on fossil fuels.
- Eco-friendly materials – Biodegradable and recyclable materials lessen environmental impact.
- Circular economy initiatives – Companies focus on reusing and repurposing materials to reduce waste.
Hyperautomation and Digital Twins
Hyperautomation combines AI, machine learning, and robotic process automation (RPA) to streamline production. Digital twins create virtual replicas of manufacturing systems, allowing businesses to test improvements before making physical changes.
Manufacturing process innovation is crucial for businesses seeking efficiency, cost reduction, and sustainability. Companies can enhance productivity and product quality by adopting automation, AI, IoT, and lean manufacturing techniques.
Investing in modern technologies ensures long-term success in a competitive market. Companies that embrace innovation will lead the future of manufacturing, driving economic growth and industry advancements.